The Integration of Robotic Manufacturing: A Practical Guide
- Deepak
- Nov 18, 2024
- 6 min read
Understanding Robotic Manufacturing
What is Robotic Manufacturing?
Robotic manufacturing involves the use of programmable machines and intelligent robots to handle tasks in the production process. These robots range from simple mechanical arms, which can perform basic tasks with a set range of motion, to complex, AI-driven systems capable of making real-time decisions based on sensor input and machine learning algorithms. By integrating these technologies, you're looking at a shift towards a more automated, efficient, and flexible production environment that can significantly reduce human labor while improving overall production quality.
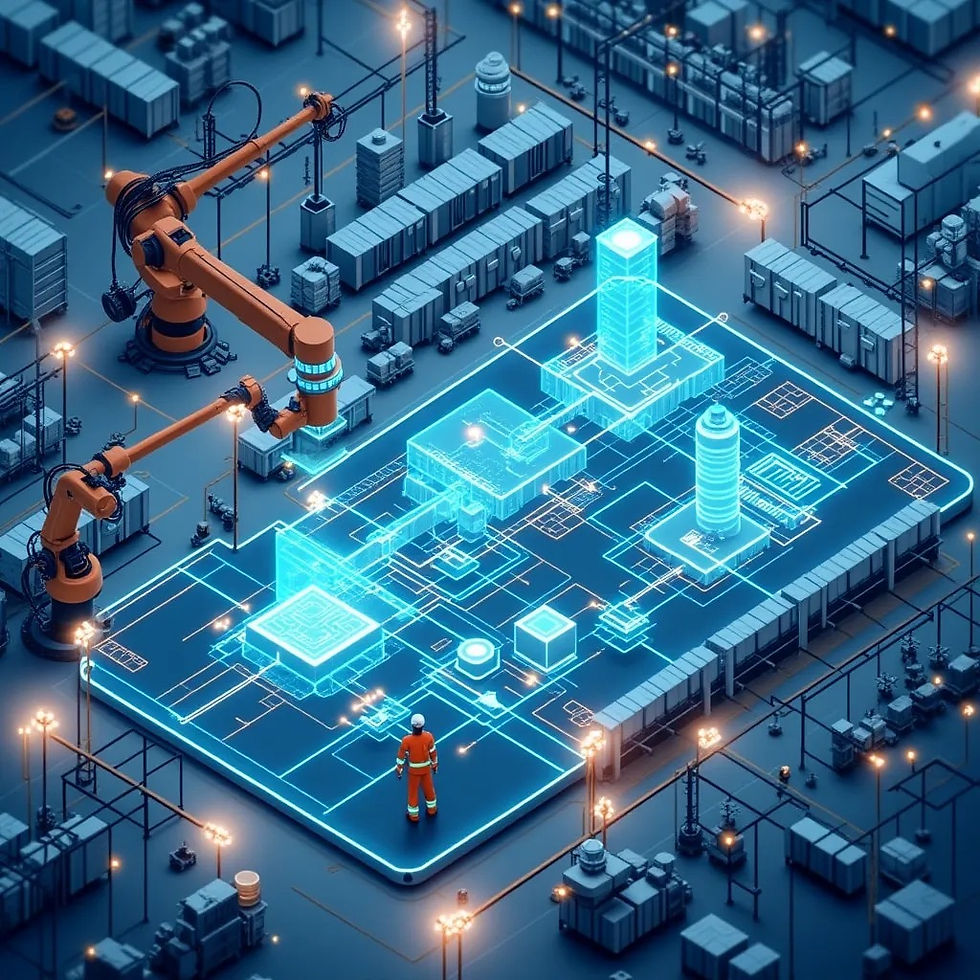
Importance in the Modern Manufacturing Landscape
The integration of robotic manufacturing is crucial in today's competitive landscape. Not only does it allow for increased precision and speed, but it also offers the flexibility needed to quickly adapt to changes in product designs or market demands. This flexibility is particularly valuable in industries where consumer preferences can shift rapidly, requiring manufacturers to pivot their operations with agility. Such adaptability enhances the resilience of your operations and enables scalability, especially important given the rapid technological advancements and fluctuating consumer expectations that characterize today's global market. Companies that adopt these innovations are often better positioned for growth and sustainability.
Trends in the Electrical Manufacturing Industry
Current Industry Trends
Staying informed about the electrical manufacturing industry trends is vital for any business striving for success. Automation and digital transformation are at the forefront, representing not merely shifts in technology but cultural changes within organizations. A significant push towards smart manufacturing and AI integration is becoming apparent, as these elements are making processes more efficient and less prone to human error. This trend is driving a new era of advanced manufacturing, where data and intelligence are not just supplementary but the backbones of operational success. Forward-thinking companies are capitalizing on these trends to gain an edge over competitors.
Role of Robotics and Automation in Electrical Assembly
Automation in electrical assembly is increasingly vital as it enhances precision, decreases lead times, and minimizes human error. Robotics' adaptability allows for installing and altering electrical components with minimal human intervention, positioning businesses to respond swiftly to changing production needs. This not only accelerates the production cycle but also ensures repeatability and reliability, which are critical elements in maintaining consistent quality standards in your products. As electrical systems become more complex, the reliability and accuracy offered by robotic solutions will likely become fundamental to achieving compliance with regulatory standards and achieving customer satisfaction.
Benefits of Robotic Manufacturing in Electronics
Process Optimization and Efficiency
With robotic manufacturing, you are empowered to optimize workflows, reduce waste, and significantly enhance process efficiency, all while freeing human workers for higher-level, value-added tasks. Advanced robotics can work tirelessly around the clock, increasing output while reducing costly downtime. This enhanced process efficiency directly translates into higher production rates and lowered operational costs, key factors for maintaining competitiveness and maximizing profits. Moreover, the data generated by robotic systems can offer insights that further refine manufacturing processes and improve supply chain logistics.
Sustainability and Advanced Manufacturing
Sustainability accompanies the shift towards robotic integration in significant ways. By reducing energy consumption and optimizing resource use, robotic manufacturing not only supports sustainable practices but also helps businesses reduce their operational costs. Implementing such technologies means that you're adopting advanced manufacturing processes that not only boost productivity but also align with global environmental standards, potentially opening new markets focused on sustainability. Companies that commit to sustainable practices are increasingly finding favor with consumers and stakeholders alike, strengthening their market positioning.
Setting Up for Successful Integration
Evaluating Your Current Manufacturing Processes
Before introducing robotics, you need a thorough audit of current manufacturing processes. Identifying inefficiencies and bottlenecks provides a clearer picture of where robotic solutions can offer significant improvements. This evaluation is crucial in transforming existing setups into lean, efficient systems through targeted automation. Furthermore, assessing your workforce's skill sets during this audit can also guide your training and development efforts, ensuring a smoother transition to integrated systems.
Identifying Opportunities for Automation
In your existing processes, determine which tasks are suitable for automation. Typically, repetitive, high-volume activities offer the greatest benefits from automation. By focusing on these areas first, you can ensure immediate improvements in efficiency and cost savings, while also laying the groundwork for more comprehensive automation strategies in the future. Additionally, considering seasonal workflow variations can help you prioritize which segments of your production line would benefit the most from robotic integration.
The Integration Process
Planning and Strategy Development
A well-structured plan is essential for integrating robotic manufacturing successfully. Define clear objectives and timelines for the implementation phases. Strategy development should consider budget allocations, software compatibility, and workforce training, ensuring that all aspects of the transition are covered comprehensively. This preparation minimizes potential disruptions and sets realistic expectations for achieving integration goals, promoting a smoother transition to robotic systems.
Selecting and Implementing the Right Technology
Choosing the appropriate robotic technology depends heavily on your specific operational needs and the scalability of your production processes. Evaluate different options based on speed, precision, flexibility, and overall cost-effectiveness. Implementing the wrong system can be costly, both financially and operationally, making it imperative to match capabilities to your manufacturing requirements. Proper technology alignment ensures optimal performance and a high return on investment, preventing costly reconfigurations down the road.
Leveraging AI for Smart Manufacturing
AI’s Role in Modern Manufacturing
AI is transforming manufacturing by providing predictive insights and automating decision-making processes that would traditionally require human intervention. Incorporating AI allows you to harness data more effectively, offering predictive maintenance, demand forecasting, and quality control that can preemptively address issues before they escalate into costly setbacks. By utilizing AI, your manufacturing processes become not just automated but intelligent, adapting to changes swiftly and efficiently, which is a significant competitive advantage as market dynamics evolve.
Examples of AI in Electric and Electronic Manufacturing
Examples of AI in practice include automated quality control systems that detect defects in electronics with higher accuracy than human inspectors, ensuring that only the highest quality products reach consumers. AI-driven robots can optimize power usage in production lines, significantly reducing your facility's carbon footprint while maintaining high efficiency rates—elements that are increasingly crucial for sustainable manufacturing initiatives. This integration not only enhances product quality but can also lead to substantial savings in energy costs.
Overcoming Implementation Challenges
Common Barriers to Integration
The primary barriers to robotic integration include high initial costs, technological complexity, and workforce resistance to change. Additionally, challenges like software compatibility and ensuring all systems communicate effectively cannot be overlooked. Addressing these barriers is essential for successful implementation and requires careful planning and communication strategies that involve all levels of your organization.
Solutions and Strategies for Successful Implementation
Addressing these challenges involves adopting strategies such as phased implementation, which allows gradual integration of robotic systems rather than overwhelming the workforce. Training your workforce in new technologies and creating an adaptive culture can ease transitions and minimize resistance, promoting acceptance and enthusiasm for the changes. Financial planning and leveraging government incentives can also help mitigate upfront costs, ensuring a smooth transition even in the face of economic uncertainties.
Measuring Success and Continuous Improvement
Key Performance Indicators (KPIs) for Robotic Manufacturing
To measure success, establish KPIs such as production rates, defect reduction, and overall equipment effectiveness (OEE). Monitoring these indicators provides insight into how well the robotic systems are performing and identifies areas for further improvement. Additionally, tracking employee satisfaction and engagement during and after the integration can provide valuable information on the human impact of changes made.
Ensuring Continuous Improvement and Digital Transformation
Continuous improvement is vital for staying competitive in an ever-evolving manufacturing landscape. Regularly analyzing performance data and integrating feedback into operations allows for ongoing digital transformation, ensuring that your manufacturing not only meets current needs but is also prepared for future challenges. This process of refinement is crucial in adapting to technological advancements and consumer demands, fostering a culture of innovation that will propel your company into the future.
The Future of Manufacturing and Executive Leadership
Future Trends in Industrial Automation
Future trends in industrial automation will likely focus on increased connectivity and smarter systems that leverage IoT devices and advanced AI algorithms. As these technologies evolve, your ability to remain agile and innovative will become increasingly significant in maintaining market leadership. Industries embracing these trends will find themselves navigating an environment that prioritizes efficiency, predictive analytics, and integrated systems more than ever.
The Role of Executive Search in Navigating Transition
Transitioning to robotic manufacturing systems requires strong leadership, capable of envisioning and driving change. Executive search plays a critical role in finding leaders who not only understand the technology but can guide your company through the complexities of integration and digital transformation. Effective leadership ensures that strategic goals are met, and operational transitions are smooth, aligning the workforce with the company’s vision for innovation and growth.
Conclusion
Recap of the Integration and Its Benefits
Embracing robotic manufacturing involves meticulous planning and implementation, offering substantial benefits like improved efficiency, sustainability, and process optimization. By integrating these advanced systems, you’re positioning your company at the forefront of the manufacturing revolution, significantly enhancing your capability to compete in a dynamic market.
Encouragement for Embracing Change and Innovation
Change and innovation may seem daunting, but they are essential for growth and resilience in a constantly evolving marketplace. Embracing advanced manufacturing technologies ensures your organization remains competitive and prepared for future industry shifts. By fostering a culture open to change and innovation, you empower your company not just to adapt but to thrive in the dynamic manufacturing landscape, setting the stage for continued success.