Crafting a Winning Manufacturing Strategy: A Step-by-Step Approach
- Deepak
- Nov 5, 2024
- 6 min read
Introduction
What is a Manufacturing Strategy?
A manufacturing strategy is a detailed plan that outlines a company's unique and methodical approach to producing goods and services. It encompasses a wide array of decisions related to technology, operations, workforce management, and supply chain management, ensuring that a business aligns its manufacturing processes effectively with its overall business goals and market demands.
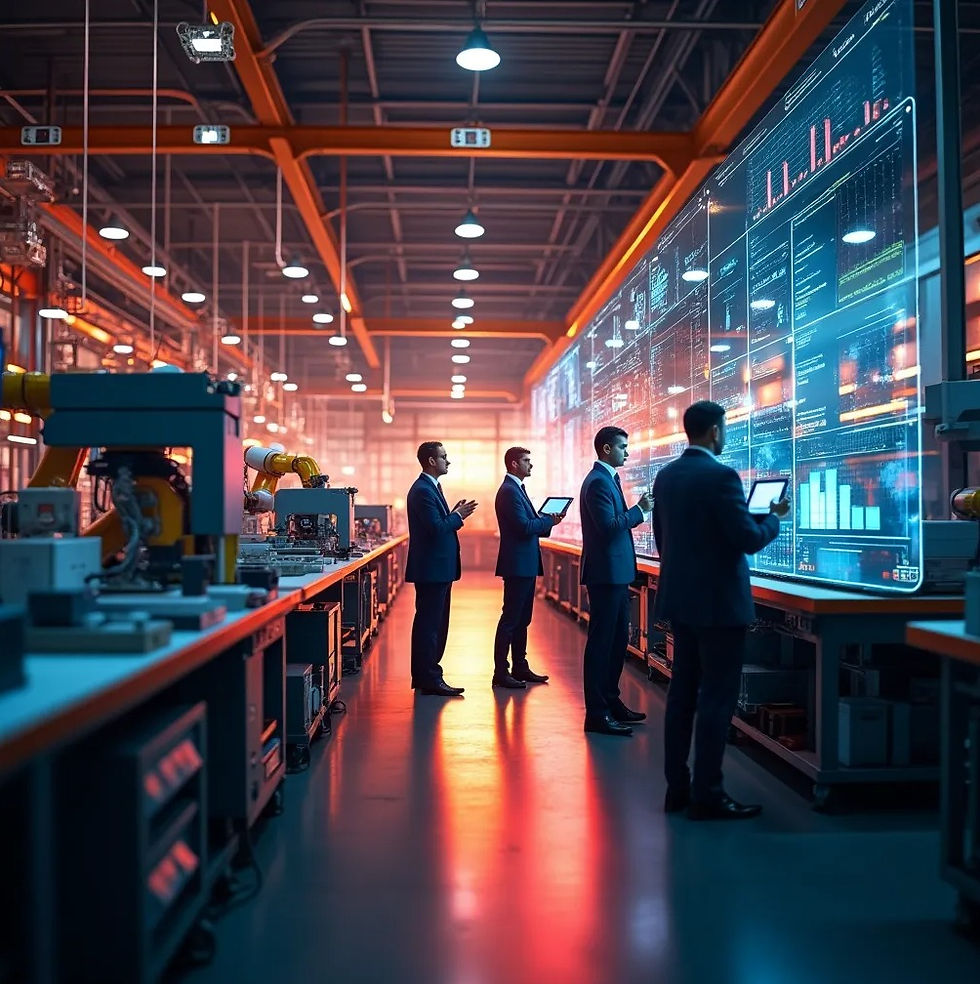
Importance of a Well-Defined Strategy
Having a well-defined manufacturing strategy is crucial for achieving efficiency, quality, and responsiveness within a business. It enables organizations to adapt swiftly to market dynamics and technological advancements, ensuring sustained competitiveness in today's fast-paced industrial environment. A well-structured strategy fosters a proactive rather than reactive approach to challenges, empowering companies to stay ahead of industry trends and customer needs.
Overview of Key Concepts: Industry 4.0, Smart Manufacturing, and More
Industry 4.0 marks the fourth industrial revolution, characterized by the seamless integration of digital technologies and automation processes in manufacturing. This transition involves concepts such as smart manufacturing, industrial automation, data analytics, and the use of artificial intelligence (AI), which are central to this transformation. Industry 4.0 promises to unlock increased efficiency, enhanced productivity, and unprecedented innovation across the manufacturing spectrum, revolutionizing how industries function.
Step 1: Assess Your Current Status
Evaluate Current Manufacturing Processes
Begin by assessing your existing manufacturing processes to identify strengths and weaknesses systematically. This thorough evaluation should focus on operational efficiency, production costs, and product quality, forming the baseline for strategic improvement. Look into production cycles, machinery effectiveness, workforce skill levels, and the overall workflow to develop a comprehensive understanding of current capabilities and areas needing enhancement.
Analyze Existing Supply Chain Management for Electronics
A comprehensive analysis of your supply chain management practices is essential, especially for electronics manufacturing, where precision and timeliness are critically important. Evaluate logistics, supplier relationships, and inventory management to streamline operations. It is also beneficial to conduct risk assessments for supply chain disruptions, ensuring that your manufacturing processes remain resilient and responsive.
Benchmark Against Industry Standards and Competitors
Comparing your processes against industry standards and competitor practices can reveal valuable areas for improvement. Utilize this benchmarking to identify gaps and opportunities that can be leveraged for competitive advantage. Assess metrics such as lead times, quality defect rates, and market share to gain insights into where your organization stands relative to the competition, thus informing your strategic decisions.
Step 2: Define Strategic Objectives
Aligning with Business Goals
Your manufacturing strategy should be closely aligned with your overarching business objectives. Consider factors such as market expansion, customer satisfaction, sustainability, and profitability to ensure that your strategy supports key business goals. Clearly articulated objectives will guide decision-making processes and provide a framework for measuring success.
Prioritizing Areas: Advanced Manufacturing, Sustainable Manufacturing, and Innovation
Focus on areas such as advanced manufacturing technologies, sustainable practices, and innovation, which are vital for future growth. Prioritize investments that will yield long-term benefits, such as reducing the carbon footprint, enhancing product quality, and improving production efficiency. Giving precedence to these areas can lead to transformative impacts on capabilities and market positioning.
Setting Measurable Outcomes
Define clear and measurable outcomes for your strategy. These may include specific targets for production efficiency, cost reductions, or environmental impact, providing a structured framework for tracking progress and success. Employing methodologies such as SMART (Specific, Measurable, Achievable, Relevant, Time-bound) objectives can further enhance clarity and focus.
Step 3: Embrace Industrial Automation and AI
Understanding the Role of AI in Manufacturing
AI in manufacturing can revolutionize how products are designed, produced, and delivered. Machine learning algorithms can optimize production schedules, enhance quality control, and predict maintenance needs, thereby reducing downtime and operational costs. By interpreting vast amounts of data, AI can also uncover trends and insights that human analysts might overlook, leading to improved strategic decisions.
Implementing Automation for Efficiency
Automation can significantly enhance productivity by reducing manual interventions and improving precision. Implement robotics and automated systems to streamline repetitive tasks, ensuring consistency and efficiency. The introduction of automated systems can also liberate skilled workers from mundane tasks, allowing them to focus on more complex problem-solving and innovation roles, thereby increasing job satisfaction and productivity.
Case Studies: Successful Automation in Various Industries
Explore case studies of successful automation implementations across different industries. These examples can provide valuable insights and strategies for deploying automation technologies effectively. By drawing lessons from these case studies, companies can tailor their automation strategies to fit their specific contexts, ensuring successful adoption and long-term investment returns.
Step 4: Incorporate Digital Transformation
Steps to Digital Transformation in Manufacturing
Digital transformation involves integrating digital technologies into all areas of manufacturing. Begin by digitizing communication, production planning, and quality control processes, laying the foundation for a fully digital enterprise. Embracing digital platforms can also enhance collaboration and visibility across all levels of the organization, facilitating a more cohesive operational strategy.
Embracing Industry 4.0 for Competitive Advantage
Adopting Industry 4.0 principles can provide a significant competitive edge. Utilize IoT, big data analytics, and cyber-physical systems to enhance connectivity, data-driven decision-making, and operational efficiency. By leveraging these technologies, you can create smarter factories that respond in real time to changes in demand and supply, leading to improved agility and responsiveness.
Utilizing Digital Tools and Platforms
Leverage digital tools and platforms for real-time monitoring and control. Utilize advanced manufacturing execution systems, digital twins, and cloud computing to optimize operations and improve responsiveness. These tools not only enhance operational efficiency but also ensure better customer service by providing accurate, timely information regarding production status and delivery timelines.
Step 5: Focus on Sustainable Manufacturing
Strategies for Reducing Environmental Impact
Develop strategies to minimize environmental impact by adopting energy-efficient technologies and materials. Implement waste reduction programs and renewable energy sources to enhance sustainability. By prioritizing sustainability in manufacturing processes, businesses can meet regulatory requirements and respond to increasing consumer demand for eco-friendly products.
Balancing Economic and Environmental Goals
Strive for a balance between economic growth and environmental stewardship. Adopt practices that reduce costs while conserving resources, such as process optimization and energy management. Engaging in sustainability initiatives can not only improve your corporate reputation but can also result in savings through resource conservation and waste reduction.
Incorporating Renewable Resources and Recycling
Incorporate renewable resources and recycling into your manufacturing processes. These practices can lower environmental impact, enhance brand reputation, and contribute to economic sustainability. Transitioning towards a circular economy approach can create additional value from existing products while addressing sustainability concerns.
Step 6: Invest in Manufacturing Innovation
Cultivating a Culture of Innovation
Foster a culture of innovation within your organization by encouraging experimentation and collaboration. Support cross-functional teams and invest in research and development to drive continuous improvement. Creating an environment where employees feel empowered to share ideas and challenge the status quo can lead to breakthrough innovations and a more engaged workforce.
Leveraging Executive Research to Drive Improvements
Utilize executive research and insights to identify emerging trends and technologies. This knowledge can inform strategic decisions and investments, ensuring your company remains at the forefront of innovation. Regularly reviewing industry reports, attending conferences, and networking with peers can provide valuable perspectives and enhance strategic foresight.
Keeping Pace with Technological Advancements
Stay updated with technological advancements and integrate them into your manufacturing processes. This will ensure your competitiveness in a rapidly evolving industry, supporting continuous growth and success. Monitoring advancements in areas such as additive manufacturing or new material technologies will allow you to leverage cutting-edge capabilities.
Step 7: Execute and Monitor the Strategy
Implementing the Strategy Across Your Operations
Execute your manufacturing strategy across all operations, ensuring alignment at every organizational level. Train your workforce and integrate new technologies to achieve strategic objectives effectively. Transparent communication about the strategy and its expected outcomes is crucial for gaining buy-in and fostering commitment throughout the organization.
Developing a Framework for Continuous Monitoring
Establish a framework for continuous monitoring and evaluation of your strategy's progress. Use key performance indicators and data analytics to track outcomes, identify potential issues, and make informed adjustments. Regularly schedule review meetings to evaluate performance against objectives and adjust course as necessary, ensuring that the manufacturing strategy remains a living document.
Adapting and Evolving with Market Changes
Continuously adapt your strategy to meet market changes and emerging opportunities. The manufacturing landscape is dynamic and subject to fluctuations in consumer preferences, economic conditions, and technological advancements. Stay agile and responsive, refining your approach to maintain alignment with industry trends and business goals, thereby promoting long-term organizational stability.
Conclusion
Recap of the Step-by-Step Approach
Crafting a winning manufacturing strategy involves a thorough assessment of current processes, defining clear objectives, embracing technology, focusing on sustainability, and fostering an innovative mindset. By following this step-by-step approach, you can ensure your manufacturing operations are efficient, competitive, and well-aligned with your overarching business objectives.
Long-Term Benefits of a Strong Manufacturing Strategy
A robust manufacturing strategy can lead to improved efficiency, cost savings, and enhanced customer satisfaction. It supports innovation and sustainable growth, ensuring your organization's success in a dynamic market environment. Companies that invest in well-defined strategies are better positioned to navigate challenges and seize opportunities in the industry.
Encouragement to Begin the Transformation Journey
Begin your transformation journey today by crafting a comprehensive manufacturing strategy. Embrace change and innovation, leveraging the principles of Industry 4.0 and sustainability to drive success and secure a competitive edge in the manufacturing landscape. Taking these initial steps can lead to substantial improvements in both operational effectiveness and market resilience over time.